Our Leadership
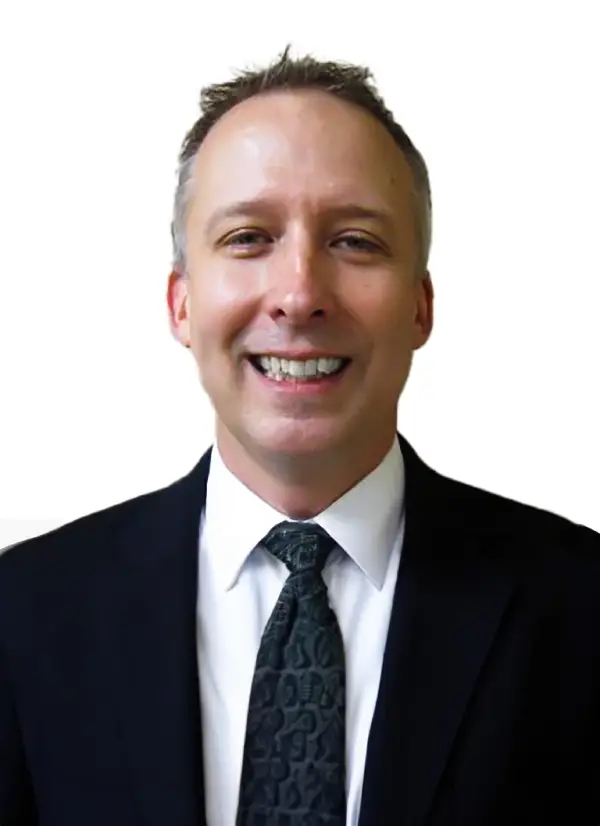
Get to know…
Dan Abney
Dan Abney is the Director of Supply Chain at Walsworth. In this role, he provides overall strategic direction for procurement and supply chain operations, develops strategic supplier relationships and negotiates agreements. The key focus is on driving best practices and synergies across the organization to maximize efficiency and achieve ongoing cost savings.
Welcome to Walsworth! Can you explain how this opportunity came about?
I saw the job posting come across LinkedIn over a weekend at a time when, I’ll be honest, I wouldn’t normally have been looking at LinkedIn. If you subscribe to “things happen for a reason,” I’ll say there’s an example right there.
As I was familiar with the Walsworth family name, and at least casually familiar with the company, I started looking a little closer.
One of our commercial sales reps here at Walsworth, Mark McCombs, is a guy I grew up with. I contacted Mark, knowing he’s been in the printing industry for his whole career and is now with Walsworth. I wanted to learn more about the printing industry, as well as the company, and Mark said this is the best company he’s ever worked for. So both the company and the opportunity to learn and apply what I know to a new industry were very appealing.
Can you describe your specific role and what it is you do?
Sure. As Director of Supply Chain, you’re providing overall direction for the supply chain and supply chain operations. And, of course, following any guidance by the company’s board of directors, and more mechanically directing procurement, purchasing operations and strategy.
It’s all about providing. Providing the materials needed, the services needed to meet whatever the organization’s requirements are. Specifically, you want quality, volume, what you want, when you need it. And last but not least, at the right pricing.
Can you tell us about your career before coming to Walsworth?
I’ve spent my whole professional career working in manufacturing companies, spanning multiple industries. First, I worked for a company called Nortek Global HVAC, which is a heating and cooling manufacturer, so air conditioners, furnaces, air handlers, things like that.
From there, I worked for a company called Maxion Wheels. They are a tier one supplier of automotive wheels. And most recently, Ingersoll Rand, who is a supplier of industrial machinery, things like air compressors, blowers, and pumps of all types.
If I think about my career, my background is technical and engineering. After building a foundation across a diversity of roles like engineering, operations, quality, maintenance and materials, I’ve spent the bulk of my career leading sourcing, procurement and supply chain teams.
Earlier when you mentioned looking into this opportunity with Walsworth, you had a personal connection that made it appealing. What about the printing industry appealed to you?
Printing is an industry I haven’t worked in but have always been interested in. And at the end of the day, it’s manufacturing. We need stuff to do what we do. We need to take the materials, transform it, add stuff, add our value and get it out the door.
Getting the ability to learn a new industry and applying what I know made this an interesting opportunity.
Many of us, not in your specific line of work, didn’t know the term supply chain until a couple years ago when the pandemic hit. Now people are more familiar. How did that event change what you do?
At the time, I was working for Gardner Denver, and we merged with the industrial segment of Ingersoll Rand in March of 2020. We basically flipped the switch, and then the pandemic hit.
And there were massive supply chain issues. For the better part of 12 to 18 months, my team wasn’t doing what we normally did, we were doing what needed to be done, which was tactically working through these supply chain issues. We had to find new sources for items. We were focused on getting materials, not necessarily saving money or other things.
It was a lot of negotiating and just trying to get supplies to mitigate lost revenue. I think what came out of that time was realizing the company’s gaps and risk.
One of my tasks then was to create a risk profile and a tool to identify where we were exposed. So we created a framework and looked at things like if we had a single source for something, can we find additional sources of supply or maybe it’s something we could make ourselves?
That thinking also fostered some acquisitions. I think it really opened eyes and people saying, “Okay, how do we maybe do some things better going forward?”
Do you feel like companies learned lessons and are better prepared if events like that happened again?
I think generally yes. I think people who lived through it and saw some of the impacts are more prepared, whether it’s by diversifying their supply base, or in some cases, putting inventory in places they didn’t have it. But I think many companies are generally in a better place in terms of risk.
Based on your observations, what do you think has allowed Walsworth to be as successful as it has been?
I think a couple things stand out. First off, the people. An organization is only as good as its people. And being here only a short while, I can definitely see the quality and commitment of the team, starting from the Walsworth family owners, down to everyone else in the organization.
That snapshot I’ve seen also demonstrates the company’s willingness to keep eyes on what’s going on in the industry and make large investments in processes and equipment. That doesn’t happen everywhere, regardless of industry. I think it’s a testament that this company is in it for the long haul.

Are you originally from Missouri?
Yeah, originally from Sedalia. I grew up there. I went to school and got my undergraduate degree at Mizzou in industrial engineering. Then around 10 years later, I completed my MBA through William Woods. And I was working and trying to help raise a family while doing that, so I definitely gained a respect for people who do that.
Can you tell us about your family?
I’ve been married to the love of my life for 35 years, my wife Patty. We have four children, Chrissy, Kevin, Robert and Leslie, in that order of age. They’re all married now and have families in various progressions of their own, which has yielded us six grandkids, four boys and two girls.
As far as things we like to do, Patty and I are pretty simple. We just like to spend time together. We like to take walks, preferably on a nice white sand beach somewhere. We love to listen to live music of various types.
Family gatherings are a big portion of what we do, where we can get all of our bunch together. That’s a big deal for us.
Are all the kids and grandkids still local?
Yeah, three of those kids and associated grandkids live in the Columbia area, and then there’s one over in Wentzville. So not too far away. They’re all in the state here, and all pretty close.
And you’re also big MU fans as well, correct?
I will say I bleed black and gold. We love tailgating and attending MU football games. We also try to make at least one road game somewhere every season and make a road trip out of that. I am also a Mizzou basketball season ticket holder. We try to have fun regardless, but if you can win a few games, that certainly makes it a lot easier. (laughs)
Beyond that, we do some volunteering. Patty did a lot of great things for a second chance high school called Whittier in Sedalia, when we lived there. So much so that she’s the only living person I know that has a scholarship named after her. Usually it’s the “(blank) Memorial whatever.” This is the Patty Abney Scholarship. We like to continue to help that organization as best we can.
What’s one thing about you people might not know?
I ended up volunteering at my church in Sedalia for several years as a sound engineer. I didn’t really know anything going into it. I am a pretty technical guy but had never done that. But each year we put on this massive community-wide service on Easter. We would get up to 5,000 people attending this thing and had to go out there and build everything from scratch in this arena on the State Fairgrounds.
And so my last year there, some other people bowed out, and I had to do this on my own. Fortunately, I drafted a skilled helper, and somehow we managed to put it all together and pull it off.
Listening to how things sound and mixing live instruments and vocals made me a better listener in general for what I do. Now, you might have to cross-check that with my wife, because she might disagree. (laughs)
Do you have a favorite book?
I would say action type things like the Robert Ludlum books, the Jason Bourne series. Those have been around a long time.
Work-wise, I like the simpler versions of lean continuous improvement titles. Like All I Need to Know about Manufacturing I Learned in Joe’s Garage. That’s a pretty thin, pretty easy read, but you can get some practical examples of how things work.
You have a favorite movie?
Yeah, that one’s pretty easy. The Blues Brothers. I’ve been known to quote that more than my family would like.
What about a favorite meal?
I would say a fresh caught Florida grouper, on a sandwich or on a plate in some way. I like that.

So you love that meal, and earlier you mentioned walking on the beach. Do you have a favorite beach vacation spot?
I can think of several. Probably my favorite was last year, just Patty and I went to Maroma Beach near Cancun, Mexico. That was a good week.
If you had a personalized coffee mug, what would it say?
I’ve had some version of this, but it was something to the effect of, “If at first you don’t succeed, call dad.” Now it might be, “call PaPa.”
As you reflect back on your career, do you have a favorite accomplishment, or favorite memory?
There’s definitely been some good ones. I think about any number of crises averted. You know, needed materials found, costs saved, bankruptcy survived, broken processes fixed.
I would also say that I’ve been part of some outstanding teams. And getting the opportunity to lead and be led by great people is what really stands out. If I think about the people I’ve been blessed to work with in the trenches, it brings back a lot of good memories.
Are there any parting messages you’d like to share?
Well, you were asking earlier about future success and growth for Walsworth and the printing industry. I was thinking about that, and I’ll have to go back to people. I definitely believe, whether it’s this organization or any other, our success is tied to empowering and growing the people.
So really, just developing and leveraging people in our organization is key to that. And I think continuing to embrace the start to finish change in this industry and continuing to take steps to support it, while also thriving in the midst of what could be future chaos as well. And certainly, this company’s willingness to make investments to support that is a huge deal.